在精密机械零件加工领域,材料的选择与加工工艺的适配至关重要。高碳钢凭借其独特的性能特点,在众多领域中有着广泛的应用,而将其与先进的 CNC 加工技术相结合,能够制造出高精度、高性能的机械零件。
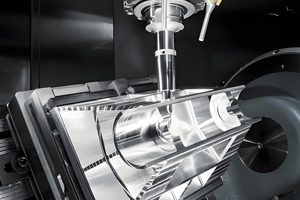
高碳钢的特性剖析 高碳钢,含碳量通常在 0.60% - 1.70% 之间。与低碳钢和中碳钢相比,其显著特点在于具有较高的强度和硬度。这是因为碳元素在钢中形成了硬而脆的渗碳体,使得钢材的整体强度大幅提升。例如,在一些需要承受高压力、高磨损的机械零件中,如模具、刀具、轴承等,高碳钢的高强度特性使其成为理想的材料选择。 然而,高碳钢的高含碳量也带来了一些加工挑战。一方面,其硬度较高,这使得在切削过程中刀具承受的切削力增大,刀具磨损加剧。另一方面,高碳钢的导热性较差,在加工过程中产生的热量难以迅速散发,容易导致加工区域温度过高,进而影响零件的加工精度和表面质量,甚至可能引起刀具的破损。 CNC 精密机械零件加工的优势 CNC(计算机数字控制)加工技术为高碳钢精密机械零件的制造提供了有力支持。CNC 加工设备通过预先编写的程序控制刀具的运动轨迹和加工参数,具有高度的自动化和精确性。在加工高碳钢零件时,能够实现复杂形状的加工,如精密的轮廓曲线、异形孔等,这是传统加工方法难以企及的。 同时,CNC 加工的重复定位精度高,能够保证批量生产的零件具有一致的尺寸精度和质量。例如,在制造一系列高精度的高碳钢齿轮时,CNC 加工可以确保每个齿轮的齿形、齿距等参数的高度一致性,从而提高整个传动系统的稳定性和可靠性。
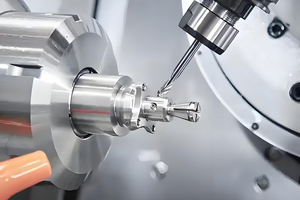
加工过程中的关键要点 刀具选择:鉴于高碳钢的高硬度特性,必须选用合适的刀具材料。硬质合金刀具是较为常用的选择,其具有较高的硬度、耐磨性和耐热性,能够在一定程度上抵抗高碳钢加工时的高切削力和高温。例如,含钴量较高的硬质合金刀具,在加工高碳钢时表现出较好的切削性能。此外,涂层刀具也是一个不错的选择,如采用 TiAlN 涂层的刀具,能够显著提高刀具的耐磨性和抗氧化性,延长刀具的使用寿命。 切削参数优化:合理的切削参数对于高碳钢的 CNC 加工至关重要。切削速度不宜过高,以避免因温度过高导致刀具磨损加剧。一般来说,根据刀具材料和零件的具体要求,切削速度可控制在较低的范围。进给量也需要适中,过大的进给量可能导致切削力过大,影响加工精度和表面质量;过小的进给量则会降低加工效率。切削深度要根据零件的余量和刀具的承载能力进行合理分配,通常在粗加工时可适当加大切削深度,以提高加工效率,而在精加工时则减小切削深度,保证加工精度。 冷却润滑:由于高碳钢加工时产生的热量较多,有效的冷却润滑措施必不可少。切削液的选择要综合考虑其冷却性能、润滑性能和防锈性能。水溶性切削液具有良好的冷却性能,能够迅速降低加工区域的温度;而油性切削液的润滑性能较好,能够减少刀具与工件之间的摩擦。在实际加工中,可根据具体情况选择合适的切削液,并采用合适的冷却方式,如内冷、外冷等,确保加工过程的顺利进行。 质量控制与检测 在高碳钢 CNC 精密机械零件加工完成后,严格的质量控制与检测是保证零件质量的关键环节。通过使用高精度的测量仪器,如三坐标测量仪、轮廓仪等,对零件的尺寸精度、形状精度和表面粗糙度进行检测。对于尺寸精度要求较高的部位,要确保其在公差范围内;对于形状复杂的零件,要检测其轮廓是否符合设计要求;对于表面质量,要保证表面粗糙度达到规定的标准。 一旦发现零件存在质量问题,要及时分析原因,如刀具磨损、切削参数不当、设备精度下降等,并采取相应的改进措施。例如,如果是刀具磨损导致的尺寸偏差,及时更换刀具并重新调整加工参数;如果是设备精度问题,对设备进行精度检测和调整,确保后续加工的质量。
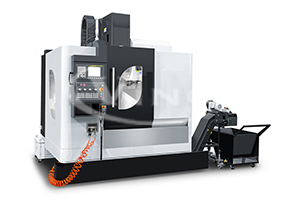
综上所述,用高碳钢进行 CNC 精密机械零件加工需要充分了解高碳钢的材料特性,合理运用 CNC 加工技术的优势,严格把控加工过程中的各个环节,包括刀具选择、切削参数优化、冷却润滑以及质量检测等。只有这样,才能制造出高质量、高精度的机械零件,满足不同行业对高碳钢精密零件的需求。