在科技飞速发展的当下,机器人已从科幻作品走进现实,广泛渗透至工业、医疗、服务等诸多领域。而这一切的背后,精密机械加工技术对机器人零件的雕琢功不可没,恰似赋予机器人灵动的“灵魂”,让其得以精准执行各类复杂任务。
机器人由众多关键零部件构成,每一个都在其运行中扮演独特且重要的角色。以关节部位为例,作为机器人实现灵活运动的核心,其中的减速器、丝杠、轴承等零件的加工精度要求极高。减速器负责将电机的高速低扭矩输出转化为低速高扭矩,以驱动关节实现平稳运动。像谐波减速器,其柔轮的弹性变形与齿啮合需高度精准,才能确保运动平稳且定位精确,这就要求精密机械加工能够将柔轮的齿形误差控制在极小范围内,表面粗糙度达到微米甚至纳米级别。丝杠则承担着将旋转运动转化为直线运动的重任,常见的滚珠丝杠和行星滚柱丝杠,在进行机器人零件加工时对螺纹的精度、导程的一致性等要求严苛。例如,行星滚柱丝杠因其传动效率高、精度高、寿命长等优势,在人形机器人的腿部关节应用广泛,其丝杠的螺纹加工需借助高精度的螺纹磨床,确保螺纹轮廓精准,滚柱与丝杠、螺母之间的配合间隙控制在恰到好处的范围,以保障传动的平稳性与可靠性。轴承作为支撑和引导旋转运动、减轻摩擦的关键部件,其加工精度直接影响机器人关节运动的平稳性和能量损耗。交叉滚子轴承在工业机器人中应用普遍,制造时需保证内外圈滚道的圆度、圆柱度以及滚子的尺寸精度和表面质量,通过精密磨削等工艺,使轴承在承受复杂载荷时仍能顺畅运转。
为满足机器人零件如此高的精度需求,精密机械加工领域不断推陈出新,涌现出一系列先进的工艺与技术。在切削加工方面,高速切削技术凭借高切削速度和进给率,大幅提升加工效率的同时,能有效改善零件表面质量。以加工铝合金材质的机器人外壳为例,高速切削可使表面粗糙度降低,减少后续打磨等工序,且能精确控制零件的尺寸精度,满足外壳对美观与装配精度的双重要求。而微量润滑切削技术,通过向切削区域精准供给微量的润滑剂,在降低刀具磨损、延长刀具寿命的基础上,保证加工精度,特别适用于对润滑要求高、对环境污染控制严格的机器人零件加工场景。在特种加工领域,电火花加工利用放电腐蚀原理,能够加工传统切削方法难以处理的高硬度、高强度材料,如在加工机器人内部一些具有复杂形状的硬质合金零件时,可通过精心控制放电参数,精准蚀除材料,实现复杂形状的成型。激光加工技术则借助高能量密度的激光束,对材料进行切割、打孔、焊接等操作,具有精度高、热影响区小的优势。例如,在制造机器人传感器的微小零部件时,激光加工可实现微米级别的打孔和切割,满足传感器对高精度、微型化的需求。此外,复合加工技术将多种加工方法集成于同一工序,如车铣复合加工,能在一次装夹中完成多种加工操作,减少装夹次数带来的误差,提高零件的整体精度和加工效率,对于制造具有复杂结构的机器人关节零件尤为适用。
在实际加工过程中,诸多因素会对机器人零件的加工精度产生影响。机床作为加工的基础设备,其精度至关重要。高精度的数控机床配备先进的数控系统,具备高定位精度和重复定位精度,能够精确控制刀具的运动轨迹。然而,机床在长期使用过程中,关键部件如丝杠、导轨等会出现磨损,导致精度下降。因此,定期对机床进行精度检测与维护保养,及时更换磨损部件,是确保加工精度稳定的必要措施。刀具的选择与使用也直接关系到加工精度。不同的刀具材料、几何形状和涂层,适用于不同的加工材料和工艺要求。例如,加工硬度较高的合金钢零件时,需选用硬质合金刀具,并优化刀具的刃口半径、前角、后角等参数,以减少切削力,降低零件表面粗糙度,保证尺寸精度。同时,刀具在切削过程中会逐渐磨损,当磨损到一定程度时,会影响加工精度,所以需要合理设定刀具的使用寿命,及时更换刀具。工件材料本身的特性,如硬度、内部组织均匀性等,也会对加工精度造成影响。对于硬度不均匀的材料,在切削过程中易产生切削力波动,导致零件尺寸偏差。因此,在加工前需对工件材料进行严格筛选和预处理,如通过退火、正火等工艺改善材料的加工性能。此外,加工环境的温度、湿度和振动等因素也不容忽视。温度变化可能导致机床和工件产生热变形,影响加工精度;湿度较大可能使机床部件生锈,降低精度;外界振动会干扰切削过程,引起刀具振动,使零件表面出现振纹,降低表面质量。所以,保持加工车间的恒温、恒湿,采取有效的减震和隔振措施,对保证加工精度十分关键。
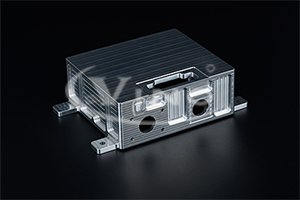
质量控制贯穿机器人零件精密机械加工的全过程,是确保零件质量的关键防线。在原材料采购环节,严格把控材料的质量,对每批次原材料进行全面检测,包括化学成分分析、力学性能测试、硬度检测等,确保其符合设计要求,从源头上保障零件质量。在加工过程中,运用先进的检测技术和设备对零件进行实时监测。例如,通过三坐标测量仪对零件的关键尺寸进行高精度测量,将测量数据与设计图纸进行对比分析,一旦发现尺寸偏差超出允许范围,及时调整加工参数。利用表面粗糙度仪检测零件表面光洁度,确保表面质量满足要求。对于一些内部质量要求高的零件,采用无损检测技术,如超声波检测、X射线检测等,检查零件内部是否存在裂纹、气孔等缺陷。在零件加工完成后,进行全面的终检,对零件的各项性能指标进行综合评估,只有通过严格检测的零件才能进入下一环节。同时,建立完善的质量追溯体系,记录每个零件在加工过程中的所有信息,包括原材料批次、加工设备、加工参数、操作人员、检测数据等,以便在出现质量问题时能够快速准确地追溯原因,采取有效的改进措施。
随着机器人技术的不断发展,对其性能和功能的要求日益提高,这也为机器人零件的精密机械加工带来了新的挑战与机遇。未来,在工艺创新方面,将持续探索更加高效、高精度的加工方法。例如,随着纳米技术的发展,纳米加工工艺有望在机器人零件制造中得到应用,实现原子级别的材料去除与成型,进一步提升零件的精度和表面质量。在智能化加工方面,借助人工智能、大数据等技术,实现加工过程的智能控制与优化。通过对大量加工数据的分析,建立加工过程模型,实时预测加工状态,自动调整加工参数,以适应不同零件的加工需求,提高加工效率和质量稳定性。同时,随着机器人在各个领域的应用不断拓展,对零件材料的性能要求也越发多样化。研发新型材料的精密加工工艺,如高强度、轻量化的复合材料,将成为未来的研究热点之一。在满足零件高精度加工要求的同时,如何降低加工成本、提高生产效率,也是行业需要持续攻克的难题。通过优化加工流程、提高设备自动化水平、合理配置资源等方式,实现精密机械加工的高效、低成本生产,以适应大规模机器人制造的需求。